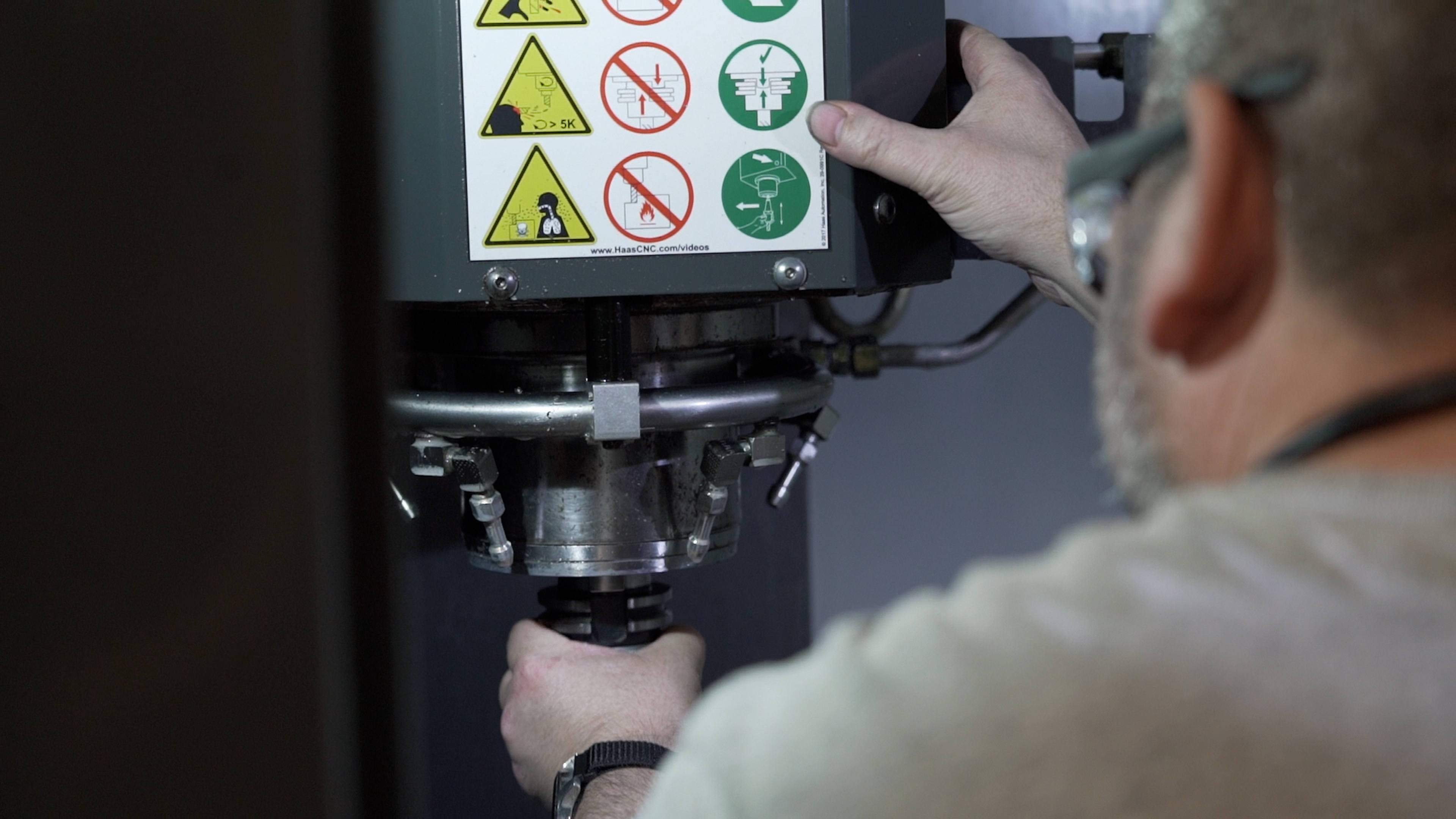
Since 1985, a northeastern machine shop has been providing high-quality, high precision parts to the electronics, defense, and medical industries. This shop, while great at making parts, was reliant on manual processes that required constant oversight, and they lacked real-time visibility. With the unprecedented rising cost of doing business, it was clear to the shop that they would need to overcome the coming economic challenges.
The Challenge
The producer price index (PPI) is a powerful tool that is commonly used to help businesses understand the trends within their industries and allows for adjustments in contracts for purchasing and sales. PPI measures the average change in prices received by consumers for a manufacturer's output. The PPI for any given industry can be so reliable that businesses will often include adjustment clauses to account for changes in prices, therefore allowing them to protect their profitability in the off-chance that price would increase appreciably.
The following table shows the PPI annual percent of increase across the last ten years for machine shops:
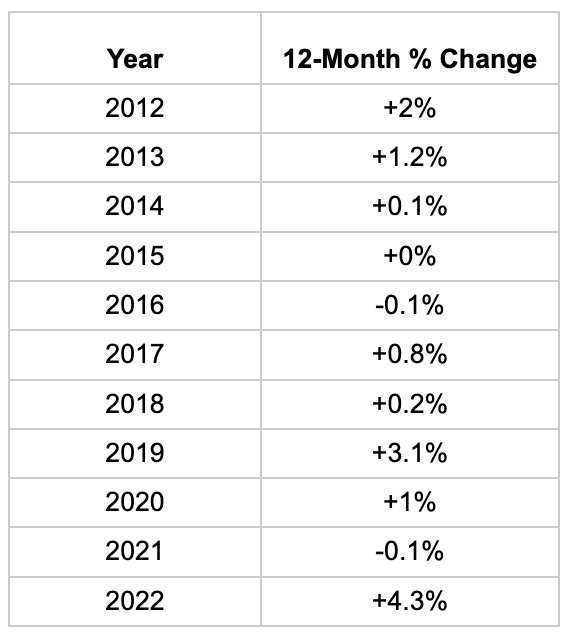
While increases in the cost of doing business can be expected when an economy is undergoing natural forces like inflation, the sudden jump in PPI for machine shops is something all owners should be aware of. This 2022 PPI jump is further visualized in the graph below:
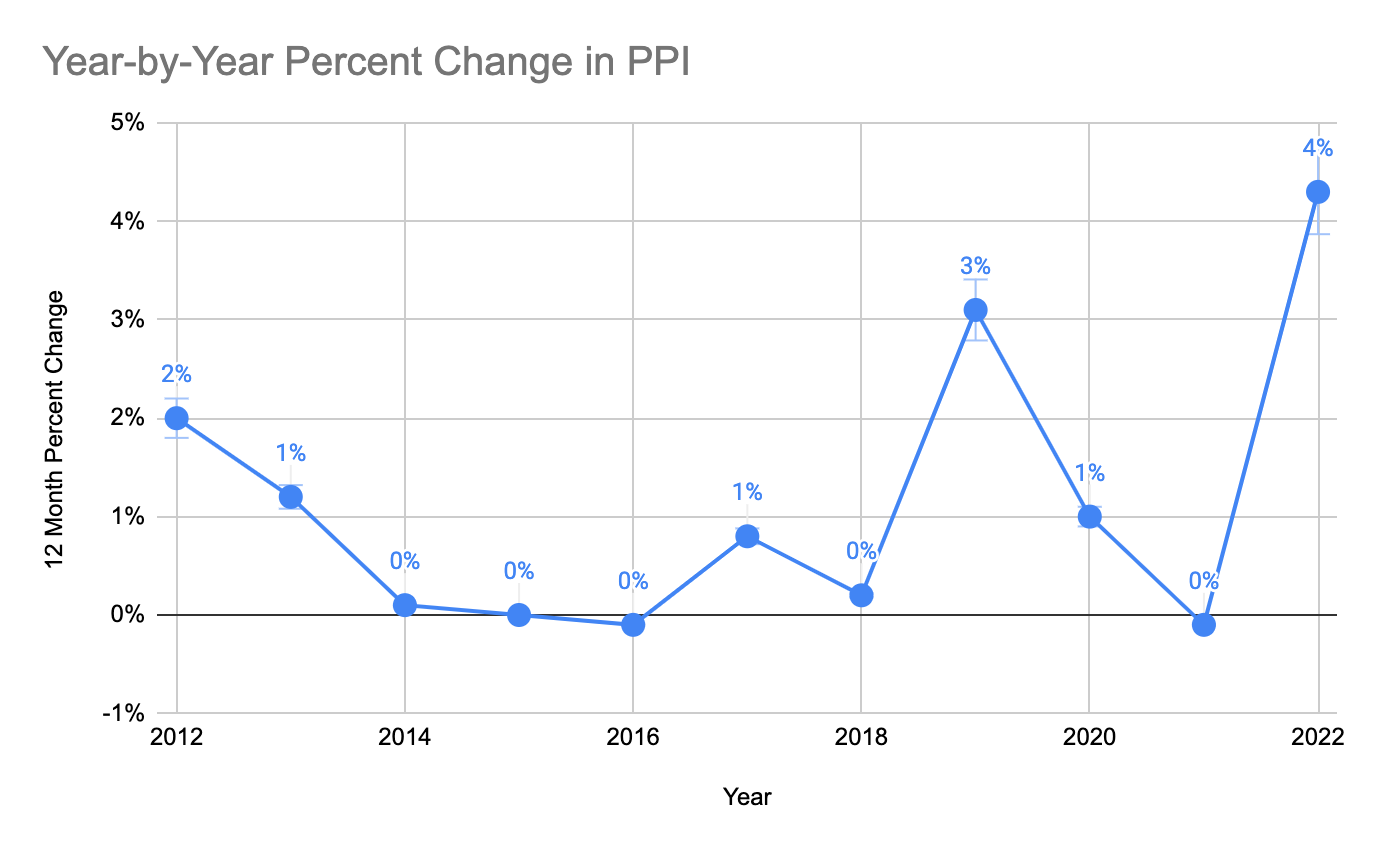
It’s clear to see the largest PPI spike in the last ten years occurs in 2022. This increase can be attributed to many things—increasing cost of labor, for one, and an increase in raw materials costs, these two things increased at an unusually fast rate in the last year. An increase in the cost of raw materials is especially significant for machine shops, which must now consider their options for keeping customer-perspective costs low, moving forward.
The Solution
In light of the latest PPI increase, this family-run machine shop utilized a manufacturing execution system blended with a lightweight ERP to dramatically improve its efficiency to help offset increased labor and raw material costs.
Time-consuming, in-person instruction for complex operations including quality control, and packing and shipping, were significantly reduced by real-time documentation updates and the digitalization of shop processes. This allowed for faster onboarding of new talent and reduced the amount of time new hires needed to learn the operations of the job floor. Providing digital real-time work instructions (e.g. with an iPad or computer) enabled massive amounts of improvement to support new and existing employees.
Job processes themselves were also updated—previously, these processes were not well documented, so this machine shop often struggled with setup pains and errors for repeat orders. These issues are common and frequently lead to lower profit margins. The StartProto software provided the shop with the means for tracking job priority, collecting digital notes, and operator discussion. While some of these are tasks that can be run manually, using software specifically designed for machine shops allows this process to be streamlined, and minimizes errors and oversights.
With the PPI spike this year, operational improvements for increased profitability can be the difference between a successful business and not. It took this northeastern machine shop only two months before they had tracked over 500 unique parts and 230 in-process work orders through the shop floor. These improvements StartProto software made to onboarding and productivity increased the shop’s capacity by $250,000 per year, while additionally allowing for an increase in overall product quality—significant improvements critical to combatting rising PPIs and competition in the manufacturing industry.
Reference
https://beta.bls.gov/dataViewer/view/timeseries/PCU3327103327100
Conclusion
Unlock the potential of AI manufacturing
Blogs & Resources
Industry trends, manufacturing business tips, and more