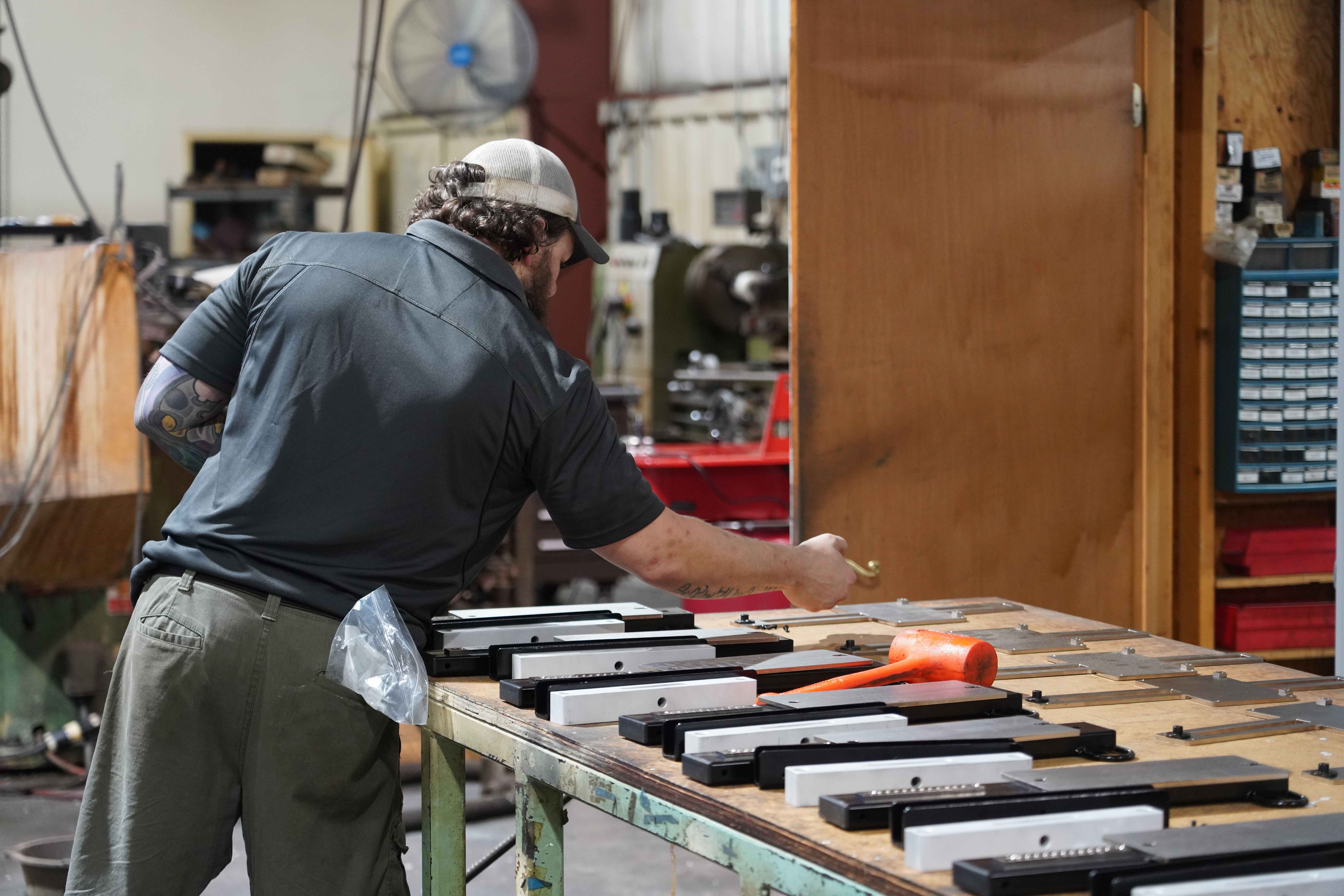
Automation dominates the conversation about the future of manufacturing, with large OEMs such as Tesla investing heavily into automation to assemble their vehicles. What’s missing from the conversation—though not from the factory floor—is humans. A Kearney study shows that 72% of factory tasks are still performed by humans (link). Despite speculation about robots replacing skilled machinists and toolmakers, there has not been significant movement toward fully automated shops. Knowing this, take a second to imagine what digital transformation looks like for a machine shop. While many solution providers have been focused on machine improvements, empowering people will add more value to the vast majority of manufacturing operations. When given the opportunity to choose a modernization strategy, StartProto urges machine shop owners to consider the following.
Human-based process improvement utilizes concepts that have been in place for many years. One of these concepts is poka-yoke (PO-ka yo-KAY). Poka-yoke, or error proofing, was developed in the 1950s as part of the Toyota Production System. Poka-yoke centers around eliminating human error, thereby making processes more effective and profitable. It outlines the following human-centric errors:
- Processing Error
- Setup Error
- Missing Parts
- Improper Parts
- Operations Errors
- Measurement Errors
The key to implementing poka-yoke is by taking a high-level approach to understanding and defining a manufacturing operation. Leaders are encouraged to clearly define machining operations, analyze failure modes, and determine how to enable operators to prevent issues through a methodical “test and measure” approach. Once all of this information is gathered, it can be used to take direct and measurable action on the shop floor.
These concepts are generally labor and time-intensive, so implementing these ideals is out of reach for the majority of manufacturers. With StartProto, we help lower the barrier to poka-yoke with rich work instructions that integrate seamlessly into their workflow. Imagine a world where everyone on the shop floor has a dedicated list of operations that need to be completed along with notes, comments from past runs, and all necessary documents. The ability for software to present job-relevant, real-time information to operators brings rapid improvements and is the key to modernizing your shop. Now, this kind of productivity can be built organically without the massive overhead of consultants and process improvement seminars for your workforce.
Conclusion
Unlock the potential of AI manufacturing
Blogs & Resources
Industry trends, manufacturing business tips, and more