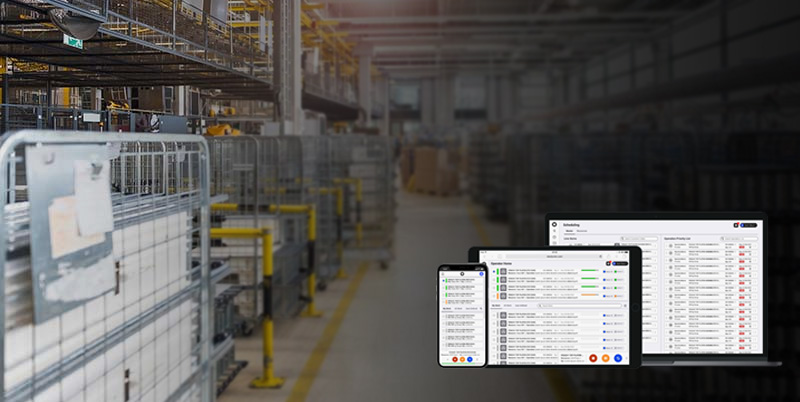
Tips for Organizing Your Manufacturing Job Shop
is your manufacturing job shop production system up to par? Technology could be a problem, but sometimes the production process structure and organization can also be significant contributing factors. Are your operators isolated in one department/in their work or cross-trained in production management?
Get real input from where it matters - no one knows the processing requirements and gaps on the floor better than the team that works there.
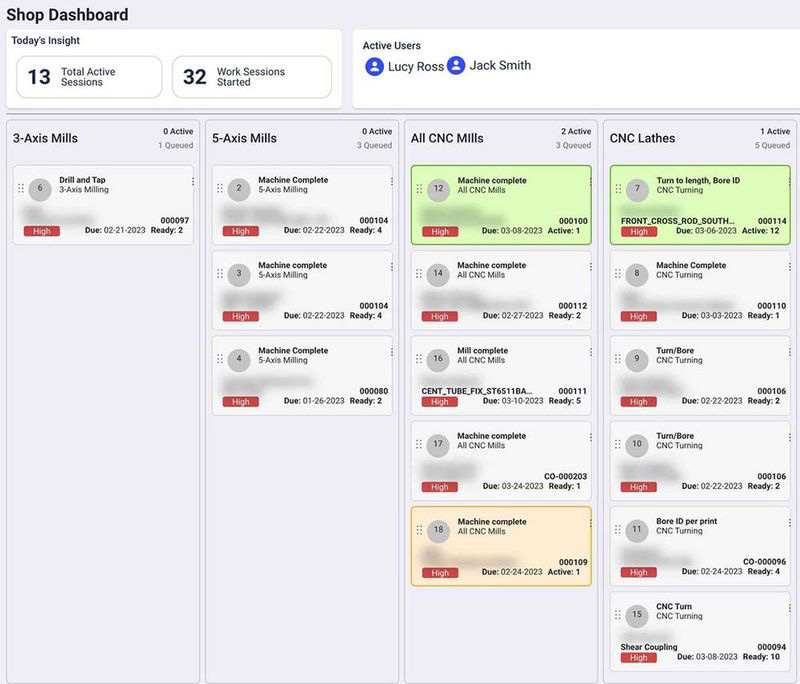
Standardize your manufacturing principles and organization - if your job, machine shop, or floor is separated into sections, ensure your manufacturing processes and organization practices remain consistent.
Why is job shop manufacturing organization important?
In today's competitive market, manufacturers must organize their job shops for various reasons.
Firstly, organizing the job shop can improve productivity, minimize waste, and optimize resources, leading to increased competitiveness.
Secondly, customers expect higher quality, faster delivery times, and more customization. Organizing the job shop can help manufacturers streamline their operations, reduce lead times, and increase flexibility to meet these demands.
Thirdly, managing inventory, production scheduling, and workflow coordination in manufacturing job shops can be complex. Organizing the job shop simplifies these tasks and reduces errors with a structured system.
Fourthly, technology advances rapidly, and businesses can leverage this to optimize processes and take advantage of real-time data and analytics. Organizing the job shop enables businesses to utilize these technologies.
Lastly, organizing a job shop helps improve workforce management by creating a structured environment that supports employee productivity and safety. This results in reduced employee turnover, minimized safety incidents, and improved job satisfaction.
Organizing a manufacturing job shop is critical today to remain competitive, meet evolving customer demands, manage complex operations, leverage technology, and improve workforce management.
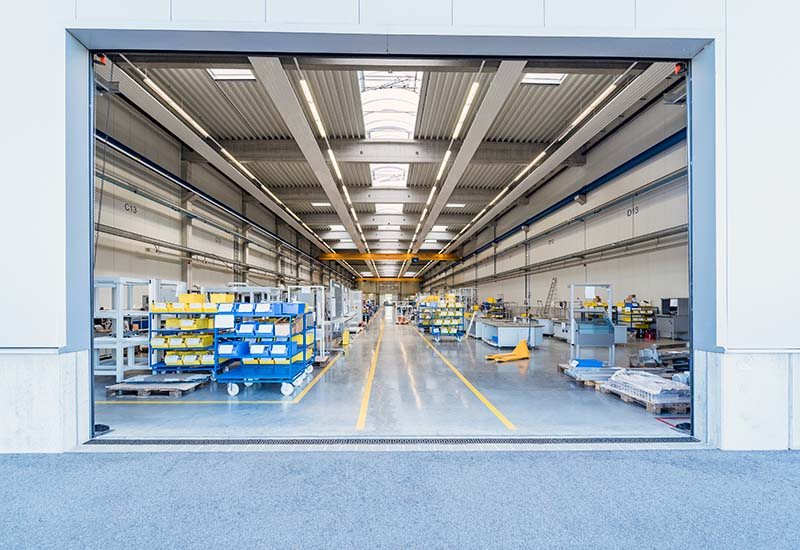
What Is a Typical Job Shop Manufacturing Process?
Job shop manufacturing or job production, is a type of manufacturing that focuses on creating unique, custom parts or products for individual customer orders.
Job shops excel at producing unique and tailored products in varying quantities or small batches per customer demand, setting themselves apart from mass production, which is geared towards churning out standardized products in large volumes.
In a typical job shop manufacturing final assembly process, the following steps are involved:
- Order Entry: The process begins when a customer places an order. The order details include the customer's specifications, requirements, and desired delivery date.
- Design and Engineering: Once the order is received, the design and engineering team reviews the specifications and develops a product manufacturing plan. They determine the materials, tools, and equipment needed to produce the product.
- Material Procurement: The purchasing department procures the necessary materials and supplies for the job, including raw materials, parts, and tools.
- Machining and Assembly: The manufacturing process begins with machining the parts according to the customer's specifications. The machined parts are then assembled into the final product. The process may involve welding, brazing, soldering, or other assembly techniques.
- Quality Control: The finished product is inspected and tested to meet the customer's specifications and quality standards. Any defects or issues are addressed and corrected.
- Packaging and Shipping: Once approved, the product is packaged and prepared for shipping. The shipping department coordinates the delivery of the product to the customer.
Job shop manufacturing system requires high levels of adaptability and precision to produce exceptional products customized to meet each customer's specific customers' unique needs.
Tips for Organizing Your Job Shop
If you run a job shop, you know that your machine worker productivity is critical to success. However, if your workers aren't performing up to par, it can be challenging to meet your productivity goals. While technology can be a problem, structure, and organization can also be significant contributing factors.
Here are some tips for managing materials organizing your job shop to ensure that your workers are productive and efficient:
1) Standardize Your Organization
If your floor is separated into small quantities or sections, ensure your organization's practices remain consistent. Consistency can help streamline operations and reduce the potential for errors. By creating standardized processes, you can ensure that everyone is following the same procedures, reducing confusion and improving efficiency.
2) Cross-Train Your Operators
Are your operators isolated in their work or cross-trained? Cross-training allows employees to learn multiple tasks, which can help them become more adaptable and productive. It can also help with team building and foster a sense of community within your organization. When employees understand how their work fits into the overall operation of small business, they are more likely to take pride in their work and make an effort to improve their performance.
3) Get Input from Your Employees
No one knows the gaps on the floor better than the team that works there. Encourage your employees to share their thoughts and ideas on improving your job shop floor's organization and productivity. Creating an environment that values employee feedback can help you identify and solve problems that might otherwise go unnoticed.
4) Use Software to Optimize Operator Tasks
Is your software tracking and optimizing operator tasks? StartProto uses x, y, and z to help streamline the needs of each job. By using software to track and optimize tasks, you can improve efficiency and reduce potential errors. Software can also help you identify areas for improvement and provide insight into which tasks are taking the most time.
In conclusion, by following these tips, you can improve the organization and productivity of your job shop. Don't let a lack of structure or organization hold your company back. Take the steps necessary to optimize your operations and simultaneously improve manufacturing performance and your bottom line. Remember, a well-organized and productive job shop can be the key to success in a highly competitive marketplace.
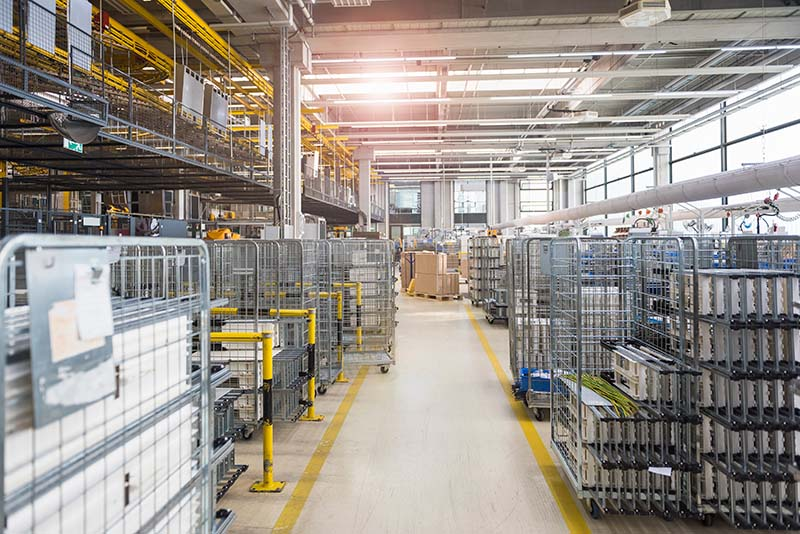
Organize Your Digital World
In addition to the above tips, digital solutions can help you organize your job shop. To address the challenges faced by manufacturing job shops, digital solutions can play a vital role. Let's explore some of the ways they can help:
Automation: Digital solutions can automate manual processes like inventory management, scheduling, and data entry, reducing errors and improving efficiency. This frees up employees' time to focus on more strategic tasks.
Data analytics: Digital solutions can collect and analyze data from various sources, providing insights into production efficiency, quality control, and inventory management. This assists managers in making data-driven decisions to optimize operations and reduce waste.
Supply chain visibility: With real-time visibility into the supply chain, digital solutions can help manufacturers manage inventory levels, monitor supplier performance, and respond quickly to disruptions.
Collaborative platforms: Digital solutions can facilitate collaboration between different departments and teams, improving communication, knowledge sharing, and workflow efficiency.
Predictive maintenance: By using machine learning and artificial intelligence, digital solutions can predict equipment failures. This enables manufacturers to perform maintenance before problems occur, reducing downtime and minimizing repair costs.
In summary, digital solutions can help manufacturers organize their job shops, improve productivity, reduce costs, and increase competitiveness in the market.
Consider a Cloud-Based ERP Tool for Manufacturing Job Shop Organization
StartProto offers cloud manufacturing software that can optimize your small to high-volume operations, manufacturing process and capacity planning, as we; as improve your bottom line. By using software to track and optimize tasks, you can improve efficiency and reduce potential errors. If one part is behind on production, the whole batch is set back, leading to high production lead time in your job shop, and low production rates. Software can also help you identify areas for improvement and provide insight into which tasks are taking the most time.
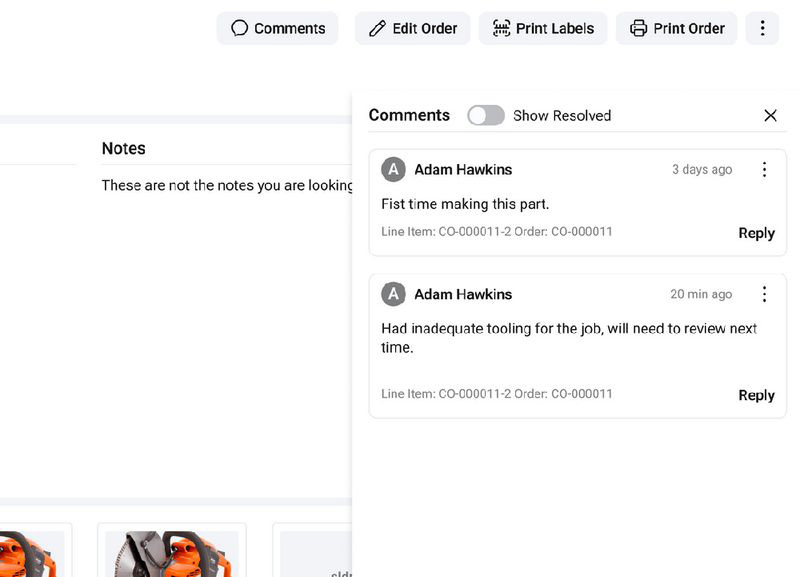
Conclusion
As a digital solution to organizing your business, consider trying StartProto's cloud manufacturing and production control software, for free today.
With a free trial, you can experience the benefits of software optimization for your job shop and see how it can improve your bottom line. Don't let a lack of structure or organization hold your company back and lose out to other businesses. Take the steps necessary to optimize your job shop and machine tool operations and improve your job shop production method for total quality control and beyond.
Unlock the potential of AI manufacturing
Blogs & Resources
Industry trends, manufacturing business tips, and more