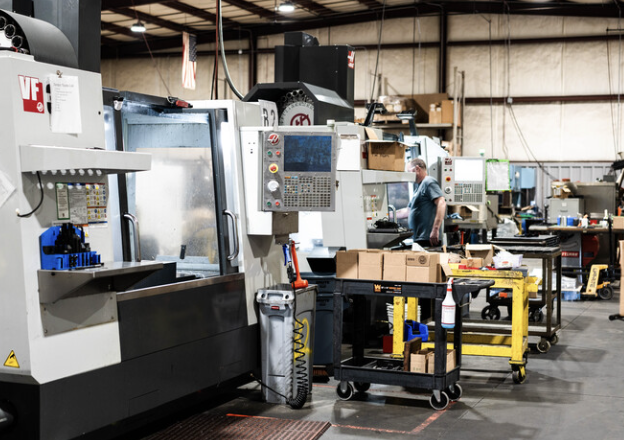
A modern machine shop will see job changes on a daily or weekly basis. The old adage "Proper Preparation Prevents Poor Performance" resonates more than ever. Often attributed to former Secretary of State James Baker, this concept, sometimes alternately quoted as “proper planning prevents poor performance,” is not just a catchy phrase but a fundamental principle that drives success in most endeavors, including running a world class machine shop.
As profit margins slim due to increasing costs from suppliers and other market factors, machine shop owners are turning to technologies like machine shop software to help streamline their front-office business operations and production schedules. The ones focusing on optimizing their planning processes and getting shipments out the door on time, are shops that prioritize work orders and decrease idle operator time.
Common Challenges in Machine Shop Management
The day-to-day operations of a machine shop are far from straightforward. They are packed with challenges that can disrupt the flow of work, causing bottlenecks, delays, and ultimately decreasing profitability. The most common hurdles are:
- Client Demands and Schedule Disruptions: Machine shops often find themselves at the mercy of client demands. Clients may change orders in terms of quantity, design, or priority, often at the last minute. This can throw a well-planned schedule into chaos, forcing the shop to juggle resources and timelines, at the cost of other orders.
- Vendor Reliability Issues: The dependency on external vendors for raw materials and outsourced items is also a critical aspect of a machine shop's operations. Unfortunately, this can be a weak link; when vendors fail to meet deadlines, it can lead to missed shipments or teams working overtime to get products out the door on time.
- Scheduling and Communication Gaps: It can be challenging to keep an updated schedule, stay on top of changes, and maintain clear communication within the shop. This is often compounded by the lack of effective machine shop management software, where key information lives in spreadsheets, post-it notes, or most commonly, tribal knowledge of the more experienced operators.
Addressing these challenges requires strategic planning, scheduling around vendor reliability issues, and allowing effective shop management software to help prioritize the schedule.
The Importance of Effective Planning in Machine Shops
Effective planning is no longer a luxury to a modern machine shop but a necessity. Failure to plan creates chaos, confusion, late shipments, which causes frustration not only at the employee level but can also erode customer loyalty and trust.
Anticipating and Managing Client Changes: By planning for variability and potential changes in client demands, machine shops can create flexible schedules and workflows that can adapt to changes without derailing the entire operation. They can also work on keeping the right inventories on hand by using predictive machine shop software to help them see their demand plans.
Vendor Relationship Management: Effective planning involves not just internal schedules but also managing relationships with vendors. This includes having backup plans and contingencies in place for vendor-related delays or issues.
Effective Communication and Documentation: A well-planned operation includes cohesive communication channels and documentation processes, ensuring that every team member is updated and aligned with the current status and any changes in the workflow.
However, the challenge lies in ensuring operators, operation managers, engineers, and sales are all aligned and on the same page. This is where the role of shop management software becomes invaluable.
Leveraging Software to Drive Profitability in Machine Shop Operations
Using spreadsheets and traveler packets may work, but machine shop software can improve efficiency in planning daily, weekly or monthly tasks for shop managers.
Efficient Job Scheduling: Effective planning and scheduling of jobs is made possible with management software which takes into account available resources and customer demands, optimizes the utilization of machines and manpower, and ensures that jobs are completed on time and within budget.
Streamlined Inventory Management: One of the core functionalities of management software is its ability to track inventory levels in real time. This helps prevent both understocking and ensuring that the necessary materials and supplies are on hand, avoiding delays.
Enhanced Production Tracking: Modern machine shop software allows for the close monitoring of each job’s progress, tracking the time spent on each task, and identifying bottlenecks or inefficiencies in the production process. These details can help management make faster decisions - leading to more products being completed and shipped on time.
Reporting and Analytics: An often overlooked aspect of management software is its ability to provide reports and analytics on various operations. This includes data on production output, resource utilization, and profitability; offering insights that drive strategic decision-making and continuous improvement.
Conclusion
The combination of these factors has resulted in significant cost savings for machine shops. With improved efficiency, better management of resources, and fewer errors, machine shops have realized that planning for constant changes can greatly enhance their financial performance.
How do you currently plan your daily operations? Are there any areas you can see that could be improved?
For real-live examples of how Startproto can help machine shops better optimize their production planning and operate in a more focused manner, look at some of our customer success stories.
Unlock the potential of AI manufacturing
Blogs & Resources
Industry trends, manufacturing business tips, and more