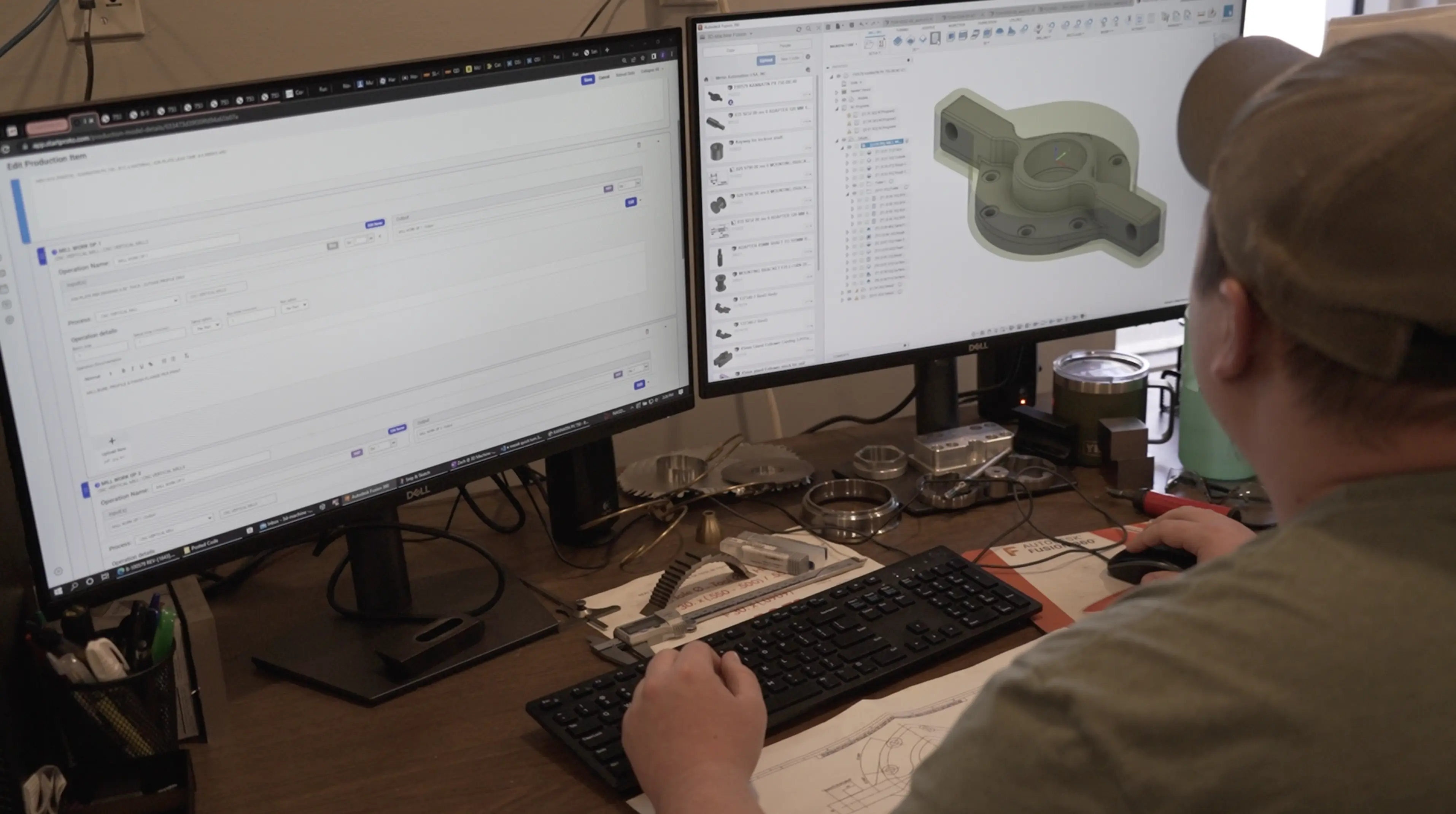
It’s said that time and tide wait for no man. The same might be said for the technology that drives the manufacturing industry. Paper forms have given way to a steady march of spreadsheets, on-premise systems, and now the age of cloud manufacturing software. All of these evolutions have saved time, improved communication, and driven overall shop efficiency.
As Joey Jones, the President and CEO of Aerotech Machining, said to Modern Machine Shop, “In this business, technology moves so fast that if you’re not changing you’re falling behind.” Keeping up with current technology, he explains, has been vital to keeping his machine shop competitive.
Streamlining production takes more these days than a three-axis CNC mill or a two-axis CNC lathe. In a separate article, MMS lists “enterprise resource planning (ERP) systems” among the six essential tools that every machine shop should have to keep up with the competition. However, even on-premise ERP software is showing its age.
Cloud-based ERP systems are the future, and they bring enormous functional benefits.
What Is Cloud Manufacturing Software?
Manufacturing software systems are designed to streamline the entire workflow of your shop, including:
- Product design and modeling (CAD/CAM)
- Quoting and sales tracking
- Work definition and routing
- Production planning
- Inventory management
- Task scheduling
- Order fulfillment
- And more
Cloud manufacturing platforms move these functions to an even more accessible and convenient format. When management can access the system anywhere in the world (in the shop, at customers' sites, or at home) and operators can pick up a tablet anywhere in the shop and scroll through detailed, step-by-step work instructions, complete with diagrams, photos, and design files, efficiency gains are a natural result.
Running a Machine Shop Online: Why Define Work From the Cloud?
You’re right — running a machine shop is not necessarily a remote job. However, the location-flexible nature of cloud manufacturing software has clear benefits for your production workflow.
Consider situations where your production manager or engineers find themselves needing to work from home a lot, for any reason — a new baby, health, travel, a hybrid schedule, or anything else. If everything they need to define items and route work is available and built out on the cloud, it will be far easier to communicate with operators and maintain visibility into what’s going on in the shop.
Even when your whole team is in the shop, modern cloud-based solutions keep everyone on the same page, from the initial quote all the way to execution. Compatible devices can access the system from anywhere in the shop and update job documentation in real-time, without time-consuming and costly on-premise installs.
Let’s take a closer look at the work definition and routing process as an example.
Optimize Your Work Definition and Routing
Too many shops still rely on paper, spreadsheets, and obsolete software solutions to define and route their work. Time-consuming manual processes and character-limited text boxes in legacy software create static and can invite misunderstandings or operator errors. This ultimately leads to more interruptions for questions, more scrap parts, and more rework.
A cloud-based system provides a smooth handoff from sales to production planning to the shop floor. Because the system handles everything about a job simultaneously — quoting, routing, material orders, task scheduling — it’s all aligned, and each step feeds the job information into the next one with no gaps. Such a seamless handoff avoids costly errors and delays.
For example, in the short video below, you can learn how to define work in a simple routing setup with StartProto, a cloud manufacturing software designed specifically for machine shops:
As you can see in the video, a cloud-based software makes it simpler to access and incorporate outside documentation, relevant design files, images, or even links to additional resources while defining items and routing work. At the same time, any items you define or route remain viewable and re-usable in future processes and other jobs — or even to reference later on when a long-standing customer returns for more of the same parts you made years ago.
The best case scenario would be for work definition to be so consistent, detailed, and straightforward that you could train a new operator in a week or less to run production of that part. This kind of plug-and-play routing is certainly easier to achieve with parts you’ve proven and produced frequently, but it can even be achieved with some prototype parts once all systems and processes have been standardized.
Embracing cloud computing in manufacturing is the first step in bringing your shop into the faster, cheaper, better operations of the future. And there’s no time to waste. Get started for free with StartProto today and see for yourself how the cloud keeps things simple.
Conclusion
Unlock the potential of AI manufacturing
Blogs & Resources
Industry trends, manufacturing business tips, and more