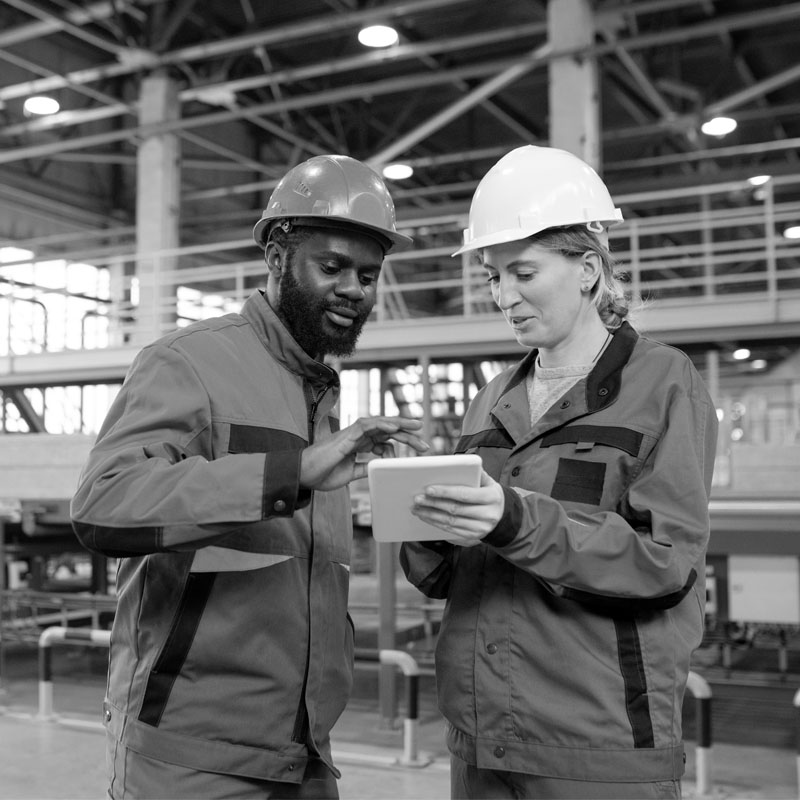
How To Improve Operational Efficiency in Manufacturing
Learn how your shop can easily increase and improve operational efficiency, without increasing the size of your team.
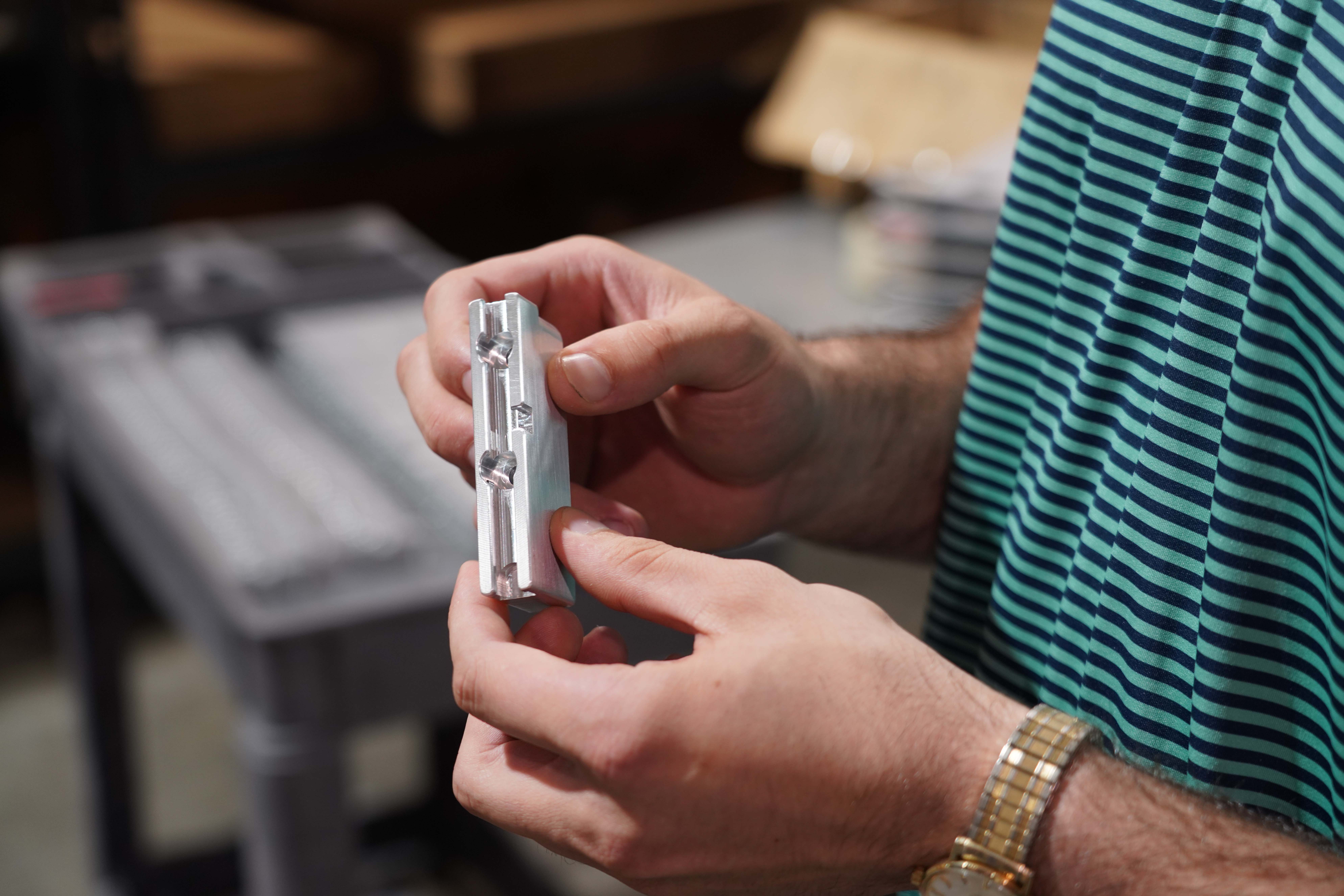
It is important to define operational efficiency for your shop. Every machine shop is unique, so there is no singular "one shoe fits all" operational improvement strategy.
However, there are some general pointers which can serve as the building blocks for helping your shop improve and maintain operational efficiency and performance.
Optimizing operational efficiency within your machine shop is a tedious and time-consuming process. It requires dedication and round-the-clock check-ins if you want to see the smallest of differences.
However, an ERP can automate operational processes, and easily regulate all these processes.
How Is an ERP Used in Manufacturing?
Enterprise Resource Planning (ERP) systems have become increasingly popular in the manufacturing industry, providing a centralized platform for managing all aspects of production.
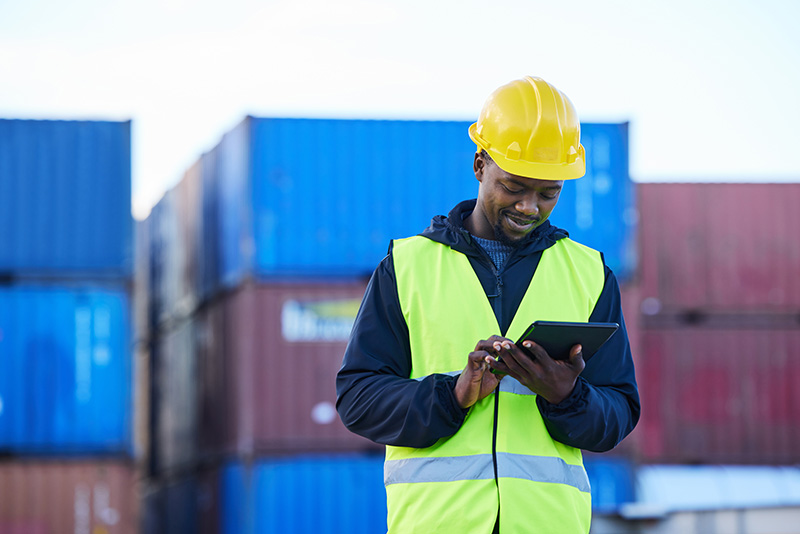
Here are some of the ways in which an ERP system can be used to increase efficiency in manufacturing:
Inventory Management
An ERP system can help manufacturers manage their inventory by providing real-time visibility into stock levels and generating alerts when inventory needs replenishment.
This can help prevent stock-outs, track capacity utilization, reduce excess inventory, and improve overall supply chain management.
Production Planning and Scheduling
An ERP system can help manufacturers to plan and schedule their production lines and activities, optimize production runs, and manage resources.
Manufacturers can ensure that orders are delivered on time and at the right cost by providing a centralized platform for managing production schedules.
Quality Control
An ERP system can help manufacturers to track and manage quality control processes, including inspections, audits, and testing.
By automating these processes and improving efficiency, manufacturers can reduce the risk of defects and improve product quality.
Cost Management
An ERP system can help manufacturers to manage costs by providing real-time visibility into expenses and automating the invoicing process.
This can help manufacturers reduce costs, improve manufacturing efficiency and profitability, and make more informed pricing and cost management decisions.
Supply Chain Management
An ERP system can help manufacturers to manage their supply chains by providing real-time visibility into supplier performance, lead times, and inventory levels.
This can help manufacturers to optimize their supply chains, reduce costs, and improve overall manufacturing efficiency further.
An ERP system is a critical tool for manufacturers, providing a centralized platform for managing all aspects of production.
By automating and streamlining manufacturing processes, manufacturers can improve efficiency, reduce costs, and improve overall profitability.
Why an ERP is Needed to Increase Operational Efficiency
The answer to this question really differs from shop to shop.
If your shop still uses pen-and-paper methods or Post-it notes, it is time to try something new.
Papers always end up either getting lost, written over, or misplaced.
Having your own production line bottlenecked because of something so trivial as a post-it note is also infuriating.
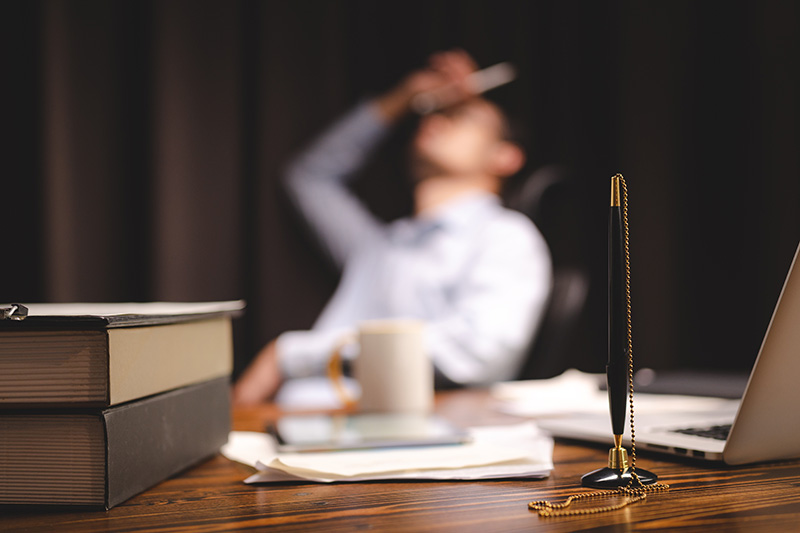
Now, for the shops and business operations that use legacy software (if you want a list of those, visit the ERP graveyard), you'll want to switch to an advanced ERP for four key reasons:
Streamlining Your Inventory Management System
The lifecycle of a part is lengthy. You need an inventory system to keep track of the materials and products. Advanced ERP systems easily manage these processes and match production with market demand.
The materials management process combines materials, tools, and techniques to create a unified lean manufacturing process.
It prevents waste of resources and eliminates instances of insufficient stock.
Gaining Real-Time Insight into Your Shop Floor
Clients expect a lot from machine shops.
For example, manufacturers must adjust their prices if the market is on a downward spiral.
At the same time, leaders of manufacturing firms want real-time updates from all sectors of the business. You can only get such utilities from an advanced ERP system.
Every element of the manufacturing process can benefit. Some of the expected benefits include real-time data transfer, data accuracy, and reliable business communications.
Consequently, partners, suppliers, and employees can have accurate visibility of the business processes' entire manufacturing process.
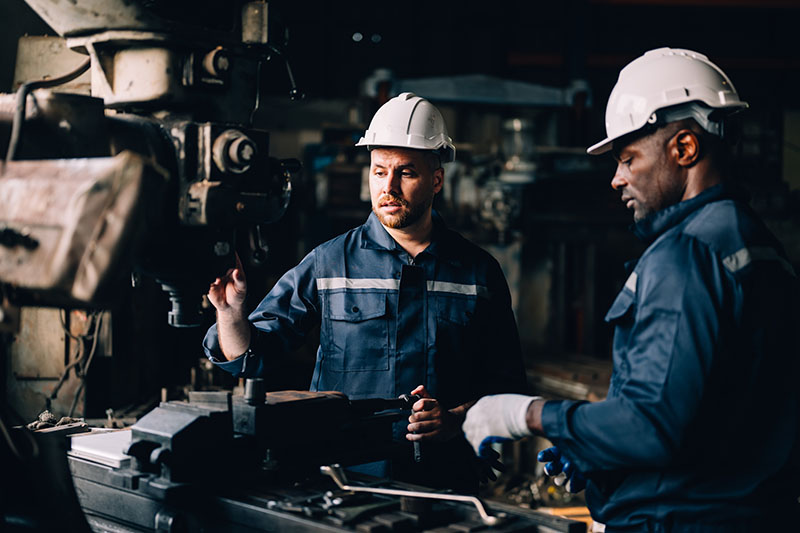
Reducing Downtime
Downtimes can create inefficiencies in production efficiency in any job shop. These operational inefficiencies will cause unnecessary delays.
You can eliminate these delays by keeping track of machine downtime. Using an advanced ERP for production planning will enhance worker shifts and workstation loads.
Increasing Security
The core software of many legacy systems is open to many vulnerabilities. This software was originally built on static systems coded in the early 2000s and 2010s.
Software systems built in the 2020s are far more secure and are necessary with updated security standards.
Picking the Right ERP to Increase Shop Efficiency
It is important first to determine what you're looking for in an ERP, whether it be simplicity, fast onboarding or advanced routing.
The only thing worse than sticking to pen-and-paper methods is choosing an ERP that is difficult to use.
Spending time learning how to use the manufacturing software, then having to train all your operators on it is only going to reduce your shop's overall operating efficiency, and waste your time.
The right ERP should be simple, intuitive, and genuinely enjoyable to use. You shouldn't have to force operators and your management team to start using it - they should genuinely want to use it.
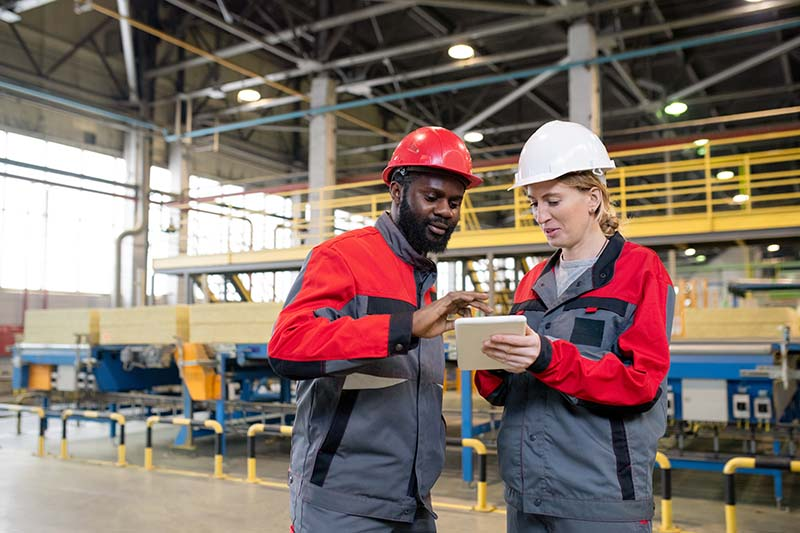
All your steps to improving operational efficiency will be ineffective if the rest of your top team members don't well receive it.
It is also important to evaluate the experiences of other machine shops that implemented the specific ERP you're interested in.
Most ERP sellers provide you with testimonials of a job well done, pages of quotes, and other marketing buzz words but most of those are done shortly after implementation.
It's very telling if an ERP vendor is able to connect you with one of their clients who can walk you through their entire experience.
Make sure you ask about ongoing support, training, and their relationship with the vendor.
Here's a snippet of what you want to look for: (if you'd like to watch the full 1-HR version, click here.)
Lastly, and most importantly, when evaluating the different ERP providers, it is important to see if the software is the "perfect fit." No ERP is a "one-size fits all" solution so there is really no way of knowing without trying it yourself. Don't be fooled by ERP providers trying to convince you with a "demo". Always remember to try it for yourself.
Before Employing an ERP to Improve Manufacturing Efficiency: Be 100% Sure.
Investing in an ERP system to improve operational efficiency is a huge step for your machine shop.
Before making a decision, remember to follow this checklist:
- Have you tried it in your shop?
- Do your operators genuinely enjoy using it?
- Is it simple and easy to use?
- Is it secure?
- Is there an easy-to-reach ongoing support team?
Every machine shop is different and it is important to find the perfect fit.
Just like you try on shoes before buying a pair, your shop needs to try out an ERP before implementing one. Try StartProto for free.
Conclusion
Unlock the potential of AI manufacturing
Blogs & Resources
Industry trends, manufacturing business tips, and more